Noticia
04-04-2024
Audi Hungría establece nuevos estándares en la producción de motores eléctricos para la plataforma PPE
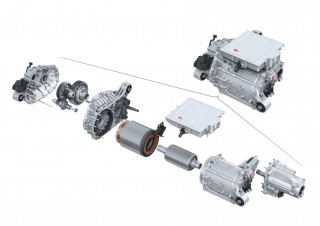
.- Para la fabricación de los motores eléctricos se han implementado tres nuevas líneas, con una capacidad de producción inicial de 2.000 motores al día
.- Los sistemas de propulsión se utilizarán inicialmente en el nuevo Audi Q6 e-tron
.- Dese 2022, alrededor de 2.000 empleados en Győr han recibido formación específica sobre electrificación
Madrid, 4 de abril, 2024 – Audi fabrica los motores eléctricos para los modelos basados en la Plataforma Premium Eléctrica (PPE) en la mayor planta de sistemas de propulsión del mundo, en Győr (Hungría). Los sistemas de propulsión se utilizarán inicialmente en el nuevo Audi Q6 e-tron, que se produce en Ingolstadt. Su fabricación en Győr se lleva a cabo en unas instalaciones con una superficie de unos 15.000 metros cuadrados, donde también se producen los componentes del estator y la transmisión, además de ensamblar los ejes. Csaba Imre Benke, Director del Segmento de Producto de Sistemas de Propulsión Eléctrica en Győr y responsable de la producción de los sistemas de propulsión para la plataforma PPE, explica cómo Audi está estableciendo nuevos estándares con este avanzado proceso.
¿Puede darnos una idea del alcance de la producción de los sistemas de propulsión para la plataforma PPE?
Csaba Imre Benke: Para producir los motores eléctricos de la PPE se han implementado tres nuevas líneas de producción. La destinada a la fabricación del estator tiene 28 estaciones de trabajo y la de componentes de transmisión, 15. El montaje de un eje requiere más de 190 pasos individuales.
¿Cuántos empleados tiene y cuántos motores eléctricos produce?
Csaba Imre Benke: En total, unos 700 empleados participan en la producción en tres turnos, y son capaces de producir 2.000 motores eléctricos cada día. Los sistemas de propulsión eléctrica que producimos aquí son los destinados a modelos basados en la plataforma PPE.
¿Qué experiencia previa tiene la planta de Győr en la producción de motores eléctricos?
Csaba Imre Benke: La producción de motores para la plataforma PPE nos obligó a aprender una serie de procesos nuevos. Cada uno de nuestros empleados necesitaron unos 20 días de formación. Pero no partimos de cero: hemos fabricado más de 500.000 motores eléctricos desde 2018. No hace falta decir que nuestra experiencia nos beneficia, sobre todo porque vamos a aumentar gradualmente nuestra capacidad de producción de motores eléctricos. En este momento estamos fabricando los estatores y las transmisiones nosotros mismos y también ensamblamos los ejes aquí en Győr.
¿Cuáles son las principales diferencias con la producción de los motores eléctricos que solían fabricar?
Csaba Imre Benke: En cuanto a la producción, el sistema de propulsión de los modelos basados en la plataforma PPE está en una liga completamente diferente. Debido a las diferencias técnicas, las líneas son distintas. Sólo para la PPE utilizamos 15 dobladoras automáticas para hacer los bobinados tridimensionales en horquilla y dos sistemas para soldar con láser los extremos. Cada estator contiene 140 metros de hilo de cobre, y se necesitan 235 soldaduras láser en total para fabricar uno. En comparación con los modelos con motor de combustión, los sistemas de propulsión eléctrica suelen tener menos fijaciones atornilladas, pero necesitan más operaciones de prensado, por lo que se pueden utilizar más robots. Además de aumentar los índices de automatización, el objetivo global es seguir aumentando nuestra capacidad de fabricación de motores eléctricos para futuros proyectos. Por ejemplo, a diferencia de lo que venía sucediendo con la transmisión del Audi e-tron, para los modelos con plataforma PPE la fabricamos nosotros mismos.
Las personas impulsan la electrificación del emplazamiento. ¿Cuánto tiempo se tarda en cualificar a los empleados para fabricar la PPE y qué niveles de cualificación existen?
Csaba Imre Benke: El primer nivel es una formación básica relativamente sencilla que lleva unas dos horas a los empleados que trabajan cerca de la línea de producción. Estas tareas no difieren mucho de la construcción de modelos de combustión. La diferencia es nuestro curso de “Sensibilización al alto voltaje” que debe realizar cada empleado. La formación destinada a la ejecución de tareas mucho más complejas dura toda una jornada laboral. Nuestros “especialistas eléctricos” reciben una formación de varios días. “Especialista eléctrico encargado” es el nivel más alto. Puede llevar unos tres meses alcanzar ese nivel, dependiendo de la formación básica del empleado. En su mayor parte confiamos en el personal procedente de nuestro área de motores de combustión. Alrededor de 2.000 empleados han recibido formación sobre electrificación en Győr desde 2022.
Características del sistema de propulsión para la plataforma PPE
Los componentes esenciales de la Plataforma Premium Eléctrica (PPE) son la batería de alto voltaje y los sistemas de propulsión. Estos últimos se fabrican en la planta de motores de Audi en Győr, Hungría. El objetivo fundamental de desarrollo era conseguir un sistema de propulsión eléctrica escalable con un alto grado de integración, eficiencia y densidad de potencia.
El sistema de propulsión de nuevo diseño consta de tres componentes principales: motor eléctrico, electrónica de potencia (inversor de modulación de ancho de pulso) y transmisión. En conjunto, cada uno de los componentes destaca por su mayor eficiencia. Están diseñados para ser escalables y más compactos. Como resultado, el par puede variar ajustando la longitud del motor eléctrico. El par en la rueda y la velocidad máxima se ven influidos en la transmisión por el acoplamiento de los engranajes. Los nuevos motores eléctricos también requieren un 30 por ciento menos de espacio. Además, el nuevo diseño ha permitido reducir el peso en torno a un 20 por ciento.
Mayor eficiencia: Una ventaja significativa de los motores eléctricos rediseñados es su eficiencia. A ello contribuyen principalmente un nuevo bobinado de horquilla en el estator, semiconductores de carburo de silicio en el inversor de modulación de ancho de pulso y una bomba de aceite eléctrica en la transmisión. El nuevo bobinado en horquilla maximiza la conducción de corriente en el estator del motor eléctrico. Este método también permite un mayor número de bobinados: la proporción de la sección del motor ocupada por el devanado de cobre es ahora del 60% en lugar del 45% que presentan los bobinados convencionales utilizados anteriormente. Gracias a la refrigeración por aceite del motor, Audi también ha podido evitar al máximo el uso de tierras raras. En total, las pérdidas causadas por la resistencia en los sistemas de propulsión eléctrica se redujeron significativamente en un 50 por ciento.
Mayor densidad de potencia: La refrigeración directa de los motores eléctricos con aceite, utilizada por primera vez, mantiene componentes como el bobinado del estator y los imanes permanentes del motor en el rango óptimo de temperatura. Como resultado, la relación peso-potencia del sistema de propulsión eléctrica PPE es aproximadamente un 60 por ciento superior a la de los sistemas de propulsión eléctrica de primera generación.
Acústica optimizada: Los nuevos sistemas de propulsión eléctrica de la plataforma PPE también destacan por su acústica especialmente silenciosa y confortable. A ello contribuyen los soportes del motor moldeados en la carcasa optimizada estructuralmente, la geometría mejorada de los dientes de los engranajes y el rotor segmentado.
Mayor integración vertical: Otro factor importante para el éxito del desarrollo de los sistemas de propulsión eléctrica de la plataforma PPE es el rango vertical de fabricación considerablemente ampliado en Győr. La mayor planta de sistemas de propulsión del mundo no solo fabrica motores eléctricos, sino también la mayoría de las transmisiones.
Motores eléctricos a medida: Al acelerar a máxima potencia entra en acción un motor asíncrono (ASM) situado en el eje delantero. El ASM no contiene imanes; genera su campo magnético por inducción y, por tanto, en caso necesario puede girar libremente sin pérdidas significativas por deslizamiento. En el eje trasero hay motores síncronos de imanes permanentes (PSM) extremadamente compactos, exclusivos de la serie Q6 e-tron.
La arquitectura de 800 voltios ahorra espacio y peso: La tecnología de 800 voltios utilizada en la PPE no sólo ofrece un alto rendimiento y tiempos de carga cortos. Como resultado de la mayor tensión eléctrica se pueden utilizar cables más finos para cablear la batería y el motor eléctrico. Esto reduce el espacio de instalación, el peso y el consumo de materias primas. Otra ventaja es la menor pérdida de calor, lo que reduce las necesidades de refrigeración.