Noticia
30-03-2021
Precisión en cada detalle: así se traslada a la producción el diseño emocional del Audi Q4 e-tron
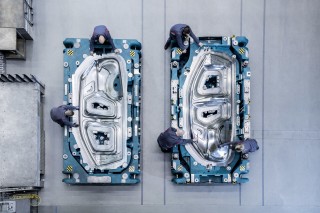
.- Las prensas, que tienen un peso de hasta 47 toneladas, ejercen una presión de hasta 1.600 toneladas
.- Cientos de piezas individuales y decenas de miles de horas de trabajo por máquina
.- El Audi Q4 e-tron hará su debut mundial el 14 de abril
Madrid, 30 de marzo, 2021 – Líneas espectaculares, superficies suaves y llamativos blisters quattro: con el Q4 e-tron, Audi da el siguiente paso en la evolución del lenguaje de diseño de sus modelos eléctricos. El SUV compacto traslada a la producción las líneas que el Audi Q4 concept presentó a principios de 2019. De ello se encarga el taller de herramientas de Audi, que permite trasladar a la producción las ideas y el sentimiento de los diseñadores con gran precisión. Una precisión que alcanza dimensiones milimétricas a la hora de construir las distintas herramientas, lo que hace que su fabricación juegue un papel crucial en los altos estándares de calidad de Audi.
Precisión cautivadora: los paneles laterales de la carrocería del Audi Q4 e-tron
De frente, de perfil o desde la zaga: el Q4 e-tron cautiva desde cualquier ángulo gracias a su expresivo diseño SUV. El panel lateral de la carrocería, que traslada a la producción las líneas del concept car mostrado en marzo de 2019, es un claro ejemplo de lo compleja que es la fabricación del vehículo. Los principales retos confluyen en una pequeña zona de la parte trasera: el pilar D se funde a la perfección con el borde lateral en la parte superior, mientras que el alerón trasero se extiende en la dirección opuesta y, más abajo, el blister, como Audi denomina a la línea que se encuentra por encima de la rueda, se extiende sobre el piloto trasero de forma pronunciada. Todas estas curvas están ejecutadas con la máxima precisión y con un acabado superficial impecable.
El responsable de ello es el equipo que compone el taller de herramientas de Audi, que traduce la visión de los diseñadores a la realidad. Sus planificadores se sientan a una mesa en las primeras fases del diseño y examinan las propuestas en función de su viabilidad. En la mayoría de los casos, la coordinación y el desarrollo se realizan digitalmente por ordenador. Para el Q4 e-tron, los equipos de los dos centros alemanes de Audi se repartieron el trabajo: los especialistas de Ingolstadt se encargaron de los paneles laterales, las puertas y el techo; mientras que el capó y el portón trasero fueron responsabilidad de sus colegas de Neckarsulm.
Un coloso de hierro fundido: 4,50 metros de largo y un peso de hasta de 47 toneladas
En el taller de herramientas, el funcionamiento más complejo se une a la precisión sin concesiones y al metal pesado. Cada una de las herramientas de prensado utilizadas para producir los paneles laterales es un auténtico coloso de hierro fundido: miden aproximadamente 4,50 metros de largo, 2,40 metros de ancho y 1,35 metros de alto, y alcanzan hasta 47 toneladas de peso. Son el fruto de decenas de miles de horas de trabajo manual y contienen hasta 500 piezas individuales, desde las correderas de alimentación y procesamiento, que pesan varias toneladas, hasta los soportes y las mordazas de conformación, pasando por las fresadoras y las perforadoras. El montaje de una sola máquina de gran tamaño lleva varios meses.
Las herramientas terminadas se instalan primero en prensas individuales de prueba y posteriormente pasan a las grandes líneas de prensas de transferencia. La mayoría de ellas comienzan este proceso en la fábrica de Audi en Ingolstadt, antes de ser transportadas a Zwickau, donde se fabrica el Q4 e-tron. Entre medias hay numerosas fases de perfeccionamiento que a menudo modifican sólo unas milésimas de milímetro. ¿Presenta la curvatura de la pieza realizada en chapa metálica una pequeña marca de hundimiento o un abultamiento inaceptable? ¿Muestran las piezas alguna disminución en su grosor apenas perceptible o diminutas arrugas en algún lugar después de cada etapa del proceso de producción? Los modernos sistemas ópticos de medición proporcionan datos exactos, pero aún no pueden sustituir la agudeza del ojo de un ser humano, la sensibilidad de sus dedos y su precepción de cómo se comporta la chapa en la prensa.
Seis etapas: producción en serie en la planta de prensado
Cuando la producción en serie está en marcha, las líneas de prensado de Zwickau necesitan un total de seis etapas para formar el panel lateral, cada una con una herramienta específica. Entre cada fase, las pinzas trasladan el componente de una herramienta a la siguiente. La primera confiere a la chapa metálica la forma deseada; y las siguientes se utilizan, por ejemplo, para recortar el metal en la zona que rodea a las ventanillas laterales, para crear los bordes y las líneas más finas, los agujeros de montaje y los complicados rebajes; es decir, los pliegues y las formas en el interior de las piezas de chapa que son necesarios para los posteriores procesos de unión en la construcción de la carrocería. Dado que la chapa tiende a contraerse ligeramente, en cada paso de trabajo se le da una nueva forma específica. Lo que en el inicio del proceso de fabricación es una chapa plana, sale al final como una pieza tridimensional realizada con el mayor nivel de precisión y un diseño emocional.
La ofensiva eléctrica acelera: el Q4 e-tron aterriza en un segmento de mercado dinámico
La ofensiva eléctrica de Audi continúa cobrando fuerza con el Q4 e-tron, que sigue los pasos de los grandes SUV, el Audi e-tron y e-tron Sportback, así como del e-tron GT de altas prestaciones. El Q4 e-tron desempeña un papel central en la estrategia de electrificación de la marca, lanzándose en un segmento de mercado especialmente atractivo y de rápido crecimiento, el de los SUV compactos. Para los clientes de Audi, supone una entrada en el mundo de la movilidad eléctrica premium a un precio competitivo.