Noticia
05-04-2017
La carrocería del nuevo Audi A8: Space Frame con una combinación exclusiva de materiales
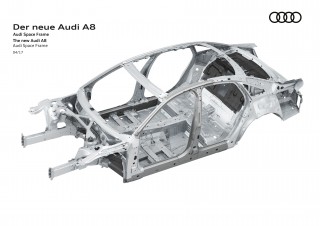
.- La nueva berlina de lujo sigue impulsando la innovación en diseño y construcción ligera
.- Nuevas técnicas y procesos de unión permiten mejorar el confort y alcanzar una extraordinaria rigidez torsional que mejora la dinámica y la acústica
.- Experiencia basada en más de un millón de vehículos producidos con carrocería Audi Space Frame
Madrid, 5 de abril de 2017 – Audi escribe un nuevo capítulo en su exitosa historia de diseño de automóviles basado en la construcción ligera. Para la nueva generación del Audi A8 se utilizará por primera vez una combinación de cuatro materiales en la estructura de su carrocería, más que en ningún otro modelo de producción hasta la fecha. La berlina de lujo de alta gama vuelve a ser pionera en construcción ligera, una tradición que se remonta al año 1994, cuando el Audi A8 causó sensación con su carrocería de aluminio Audi Space Frame (ASF).
Los expertos en construcción ligera de Audi abandonaron hace mucho tiempo la construcción convencional de carrocerías de automóviles utilizando un único material Con una combinación de aluminio, acero, magnesio y polímero reforzado con fibra de carbono (CFRP), han establecido una nueva etapa en la aplicación de múltiples materiales para la fabricación de la carrocería Audi Space Frame (ASF) en la nueva generación del Audi A8, siguiendo el principio “el material adecuado en el lugar correcto y en la proporción adecuada”.
Audi aplica constantemente nuevas tecnologías de materiales y diseños que benefician directamente al cliente no sólo en términos de peso. La rigidez torsional del nuevo buque insignia de la marca, el parámetro crítico de cara al confort acústico y el comportamiento dinámico, supera los valores de su predecesor en aproximadamente un 25 por ciento
Innovador proceso de producción: panel trasero en fibra de carbono
En términos totales, el componente más grande que conforma la célula del habitáculo del nuevo Audi A8 es un panel trasero de alta resistencia y elevada rigidez torsional realizado en CFRP, que contribuye en un 33 por ciento a la rigidez torsional del vehículo. Para absorber de forma óptima la cargas longitudinales y transversales, así como las fuerzas de deformación, en la fabricación de este panel se colocan entre seis y diecinueve capas de fibras una encima de la otra, garantizando un diseño optimizado de cara a soportar las cargas. Estas capas de fibra individuales están formadas por cintas de 50 milímetros de anchura que pueden colocarse en finas capas formando cualquier ángulo y con un recorte mínimo. El innovador proceso de estratificación en capas de las fibras, diseñado especialmente para este propósito, permite prescindir por completo del paso intermedio normalmente necesario a la hora de fabricar paneles completos de fibra de carbono. Utilizando otro proceso también de nuevo desarrollo, el panel resultante se cubre con resina epoxi y se somete a un proceso de curación que dura apenas unos minutos.
La estructura de la célula de habitabilidad que conforma el habitáculo está realizada con una combinación de componentes de acero de alta resistencia, que comprenden la sección inferior del mamparo delantero, los travesaños laterales, los pilares B y la sección delantera del techo. Algunos de estos elementos de chapa metálica se fabrican a medida en diferentes espesores, mientras que otros se someten a un tratamiento térmico parcial. Esto reduce el peso y aumenta la resistencia, principalmente en áreas del vehículo que resultan particularmente críticas para la seguridad.
Componentes de aluminio en forma de nodos fundidos, paneles y perfiles extruidos, elementos característicos del diseño Audi Space Frame, constituyen la mayor parte de la estructura de la carrocería del nuevo Audi A8, con un 58 por ciento. Y aquí también la competencia de los materiales ha impulsado el progreso: las nuevas aleaciones de fundición tratadas térmicamente, por ejemplo, alcanzan una resistencia a la tracción de más de 230 MPa (megapascasles). El límite de elasticidad correspondiente en los ensayos de tracción supera los 180 MPa, y para los perfiles se sitúa entre 280 y 320 MPa, valores significativamente superiores a los conseguidos con anterioridad.
Completando la inteligente combinación de materiales empleada se encuentra la viga de refuerzo de magnesio, que en comparación con el modelo predecesor permite un ahorro de peso del 28 por ciento. Pernos de aluminio aseguran la conexión con las torretas, contribuyendo a garantizar la alta rigidez torsional. En caso de colisión frontal, las fueras generadas se distribuyen a tres elementos de absorción de impactos en la zona delantera.
Beneficios para el cliente y en entorno – el nuevo taller de carrocería para el Audi A8
Además del rediseño completo del Audi Space Frame para la próxima generación del A8, los talleres para la producción de carrocerías del nuevo buque insignia de la marca de los cuatro en Neckarsulm también se han construido específicamente. Sólo para la construcción de la nueva instalación, de 41 metros de altura, han sido necesarias 14.400 toneladas métricas de acero, el doble del utilizado para la Torre Eiffel en París.
En el proceso de producción altamente eficiente se utilizan hasta 14 métodos diferentes de unión y ensamblado, incluyendo el engatillado por roldana para las puertas. Este proceso mecánico de ensamblado en frío se utiliza para unir los marcos de aluminio a la chapa de acero de ultra alta resistencia conformada en caliente que se utiliza para fabricar los pilares B, la línea del techo y los umbrales. Los ingenieros realizaron así mejoras de hasta 36 milímetros en los recortes de la silueta de las puertas en comparación con el modelo predecesor, lo que a su vez hace que entrar y salir del coche sea aún más cómodo y amplía el campo de visión del conductor alrededor del pilar A, un aspecto clave para una conducción segura.
En cuanto a los procesos de unión en caliente, Audi se convierte en el único fabricante premium de automóviles en utilizar la soldadura de aluminio con láser de forma remota, un nuevo desarrollo. El posicionamiento exacto del rayo láser en relación con el cordón de soldadura reduce considerablemente el riesgo de rotura en caliente de la soldadura debido a que el calor generado puede controlarse con precisión. El tamaño de la separación entre las partes a unir puede así determinarse de forma inmediata y rellenarse eficazmente mediante estrategias de control del proceso. La alta velocidad de alimentación del rayo láser y el bajo consumo de energía reducen las emisiones de CO2 aproximadamente en un 25 por ciento.
Este nuevo proceso también da como resultado un ahorro de un 95 por ciento en los costes recurrentes en la producción en serie, ya que elimina la necesidad de los costosos controles requeridos en un proceso convencional de soldadura por láser. La tecnología de soldadura remota mediante láser representa a la perfección la innovación aplicada en la producción del nuevo Audi A8.
En 1994 fue la primera generación de este sedán de lujo, con su carrocería de aluminio, la que hizo que la construcción Audi Space Frame se estableciera como una referencia en la industria automotriz. Desde entonces la compañía ha fabricado más de un millón de automóviles de acuerdo con este principio de diseño, y ha avanzado de forma continua en su conocimiento y experiencia en la utilización de materiales y técnicas de unión.