Noticia
13-03-2012
Audi MSF: construcción ligera con tecnología de materiales múltiples
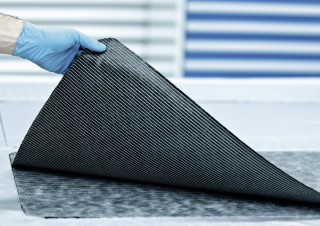
.- La tecnología MSF (Multimaterial Space Frame) consiste en combinar las ventajas de varios materiales para construir carrocerías todavía más ligeras.
.- La clave en la reducción de peso será el plástico reforzado con fibra de carbono (CFRP) en sustitución del metal.
.- Los muelles de suspensión FRP (plástico reforzado con fibra de vidrio) debutarán en el Audi R8 e-tron.
Madrid, 13 de marzo de 2012.- A principios de los años ‘90 Audi se convirtió en la marca automovilística líder en construcción ligera con sus carrocerías de aluminio. Utilizando el principio de construcción ASF (Audi Space Frame) en los Audi A8, Audi R8 y Audi TT se reduce el peso final de la carrocería en hasta un 40 por ciento comparado con las estructuras convencionales de acero. Ahora, Audi pone en marcha la siguiente etapa en el proceso: la tecnología Multimaterial Space Frame (MSF), que combina aluminio, acero y componentes CFRP.
Benjamin Bender lidera el proyecto MSF que Audi lleva a cabo en el Centro de Diseño y Construcción Ligera de Audi (ALZ) en la factoría de Neckarsulm. MSF son las siglas de Multimaterial Space Frame, una tecnología con un gran potencial de futuro: en fechas próximas, cuando las nuevas estructuras híbridas de metal y plástico reforzado con fibra de carbono (CFRP) entren en producción en serie, representarán un nuevo paso adelante en la construcción ultra-ligera de Audi, pues combinando las ventajas de varios materiales, las nuevas carrocerías serán mucho más ligeras que las estructuras fabricadas únicamente con metal.
El proyecto de Benjamin Bender convierte los componentes individuales en “componentes híbridos”. Si un elemento metálico de la estructura –por ejemplo un pilar o el umbral de una puerta– se refuerza con CFRP, se mejoran sus propiedades, como por ejemplo su resistencia o su comportamiento a la hora de deformarse en caso de un choque. Y al mismo tiempo se reduce el peso, porque comparativamente, el metal –acero o aluminio– se sustituye parcialmente por CFRP, un material mucho más ligero.
El método utilizado para unir los dos materiales como el metal y el CFRP es uno de los temas que requieren máxima atención. Normalmente esta unión se realiza con remaches, tornillos o adhesivos técnicos, pero el nuevo proyecto adopta un enfoque mucho más ingenioso: la resina sintética necesaria para producir un componente enteramente en CFRP actúa como medio de unión.
Bender investiga actualmente si es posible utilizar procesos de moldeo por transferencia de resina (RTM) para unir los dos materiales. El proceso RTM es perfectamente válido para volúmenes altos de producción en serie, y es una de las tecnologías clave en el Centro de Diseño y Construcción Ligera de Audi. “Incluso si el proceso de desarrollo va según nuestros planes, todavía necesitaremos algunos años antes de que esté listo para la producción en serie.”
Muelles helicoidales FRP
Pero para Audi, el diseño ultra-ligero resulta especialmente interesante en el área del chasis y las suspensiones. Cada reducción de peso no suspendido mejora el confort y el manejo, y en este sentido resulta especialmente interesante el proyecto que lidera Joachim Schmitt, dedicado a un componente que en principio no parece tener nada de especial, pero que soporta cargas muy severas: el muelle helicoidal. Este proyecto aspira a sustituir los convencionales resortes fabricados en acero por otros realizados en plástico reforzado con fibra de vidrio (FRP).
El muelle de FRP desarrollado por Schmitt junto al titular de la patente SOGEFI es muy diferente a un resorte de acero convencional. De un color verde brillante, el diámetro del elemento que forma el muelle es mucho mayor, y el muelle completo tiene menos espiras. Pero por encima de todo, este tipo de muelle es mucho más ligero. El ingeniero Schmitt tiene los datos: “cada uno de lo resortes de acero de la suspensión delantera de un Audi A4 pesa2,66 kilogramos, mientras que el muelle de FRP pesa sólo1,53kilogramos, una reducción superior al 40 por ciento, aunque funciona igual de bien.”
Si se diseña con este propósito en mente, un muelle hecho de plástico reforzado con fibra de vidrio es capaz de absorber muy bien las cargas de torsión. El núcleo del muelle consta de fibras de vidrio enlazadas en forma de hélice impregnadas con resina epoxi. Una máquina envuelve este núcleo, de apenas unos pocos milímetros de diámetro, con fibras adicionales entrelazadas en ángulos alternos de 45 grados respecto al eje longitudinal. Las cargas torsionales se convierten en estas fibras en cargas de tracción y compresión.
La fase siguiente en la producción del “alambre” con el que se fabrica el muelle consiste en enrollar con este componente de fibra de vidrio mientras todavía está blando un núcleo de una aleación metálica con un bajo punto de fusión. Este núcleo sería el negativo del muelle terminado. El material FRP se endurece en un horno calentándolo a una temperatura de más de 100 grados, de forma que el núcleo metálico se derrite. Este es el proceso utilizado actualmente para fabricar prototipos. Más adelante, el proceso a gran escala será mucho más rápido y más eficiente, alcanzando el millón de muelles anualmente.
Los nuevos muelles de FRP debutarán antes de finales de 2012 en el Audi R8 e-tron de propulsión eléctrica. Durante 2013, se introducirán paso a paso en modelos Audi de gran volumen, de tamaño medio y grande. Actualmente se están llevando a cabo ensayos y ciclos de pruebas maratón en dispositivos especiales, cada uno de los cuales impone cargas en el muelle equivalente a unos300.000 kilómetros, el promedio que realiza un cliente con su vehículo.
“Al principio, muchos de mis colegas dudaban del éxito del proyecto”, recuerda Joachim Schmitt. “Pero desde el principio, el material FRP está demostrando ser una excelente elección. Es absolutamente inmune a la corrosión, incluso si resulta golpeado por piedras que saltan de la carretera, y también resiste a productos químicos, como los que se utilizan para la limpieza de las ruedas. La fabricación de resortes de FRP consume menos energía que la de los muelles de acero, y su utilización reduce el peso de un vehículo como el actual Audi A4 en unos cuatro kilogramos. Un notable paso hacia delante”.
En pocos años los ingenieros esperan mejorar los métodos de producción para aumentar la capacidad de carga del material FRP, de forma que el espacio necesario para montar un muelle de este material no sea mayor que el que hoy en día necesitan los resortes de acero. En cuanto al inusual color verde brillante, los ingenieros de desarrollo también han abordado este tema. Joachim Schmitt asegura: “Si añadimos cierta cantidad de grafito a la mezcla de FRP, se tiñen de color negro. ¡Y para los conductores más entusiastas, ya trabajamos en muelles de colores azul o rojo!”